Clean-In-Place Products
Demand Clear Evidence
When is your plant not performing at its peak? When it’s down for cleaning. But what if, after all that time accumulated, your cleaning process turns out less-than-effective? That’s a revealing issue.
An effective clean-in-place process hinges on knowledge. We arrive at your plant to help you find what works. Over time, we stay in touch with your process to make sure what works performs even better.
For the Ethanol Industry
EXCELON 210 Case Study

Water drop without a surfactant (note how droplet stands up).
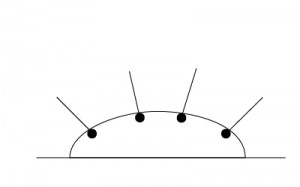
Water drop with a surfactant.
Reduce Surface Tension for a Cleaner Clean
That little fill-port inside your kitchen’s dishwasher tells the story. Add a surfactant and residue slides down the drain. No surfactant? Count on unappetizing spots of grime firmly adhered to plates and glasses at the end of the wash cycle.
In the same way, your standard caustic CIP cleaning solution will benefit from a surfactant. A cleaning solution prefers to stick to itself, holding soils in a tight grip. Excelon 210 employs proven antimicrobial technology to loosen that hold, reducing surface tension to increase soil suspension. Excelon 210 assures your cleaning cycle accomplishes more.
Excelon 210 Puts CIP On the Clock
Before Golden Triangle Energy adopted Excelon 210 from Mist Chemical, the Craig, Missouri, plant shut down 156 hours per year to clean its evaporators and stripper column. Reducing that extra time investment shaved expenses, too.
Previous to employing Excelon 210 caustic additive package, cleaning ate up 12 hours at a time. Operations Manager Shaun O’Riley reports, “With Excelon 210, the downtime decreased to four hours per cleaning. Excelon reduced our downtime and reduced our frequency of cleaning.”
Golden Triangle Energy adds Excelon directly to its CIP batch, according to O’Riley. He can do that with confidence because “It’s nontoxic, noncorrosive and approved safe for animal feed by the FDA and Center for Veterinary Medicine.”
O’Riley estimates the plant cut caustic chemical usage by 38%, a current annual savings of $101,000.
* Contact us for complete test results.
* What about your cooling tower and mash headers? We’ll design a specific cleaning package tailored to your particular plant design. All you have to do is request a consultation.